Fluidisation is the process of moving, transporting or treating powders and other granular materials by the injection of air to make the powder act as a fluid.
The air passes through a porous material where it is finely distributed and creates a cushion or film to considerably reduce the friction between material and base. In addition, the air is mixed with the material in such a way that the friction between the particles is reduced, allowing the material to flow like a fluid.
Experience has shown that porous ceramic tiles, used as the permeable membrane through which air is injected and which also supports the powder bed, provide the most efficient means of ensuring the even dispersion of air, which is essential to the success of an operation.
One such application can be found within the production process of plaster (stucco) and in particular, the transfer of newly created plaster through the process. CSR Limited, a leading building products company based in Australia whose brands include Gyprock plasterboard, utilises Mantec’s porous ceramic tiles within this process.
In CSR’s operation, crushed gypsum is fed to a kettle where it is heated to high temperatures. A chemical transformation takes place, whereby the gypsum is converted to plaster through the application of heat and removal of water molecules. The plaster then overflows to the ‘kettle hot pit’, a large receiving receptacle with a sloped floor, into which Mantec’s porous ceramic tiles are installed.
The tiles are secured into a fabricated steel frame which incorporates a compartment, or plenum chamber, below.
Low pressure air is fed into this chamber and can only escape by way of the porous ceramic tiles into the powder above, which induces fluidisation. This causes the fluidised plaster to flow under gravity toward the outlet.
From the outlet, the plaster is conveyed via an air slide to the bucket elevators, from where it is conveyed to storage silos ready for consumption on the plaster line.
Mantec’s porous ceramic tiles are subject to close quality control during manufacture. Individual tiles are matched one against the other to ensure even overall permeability and the grades used present sufficient resistance to spread the air evenly over the whole area.
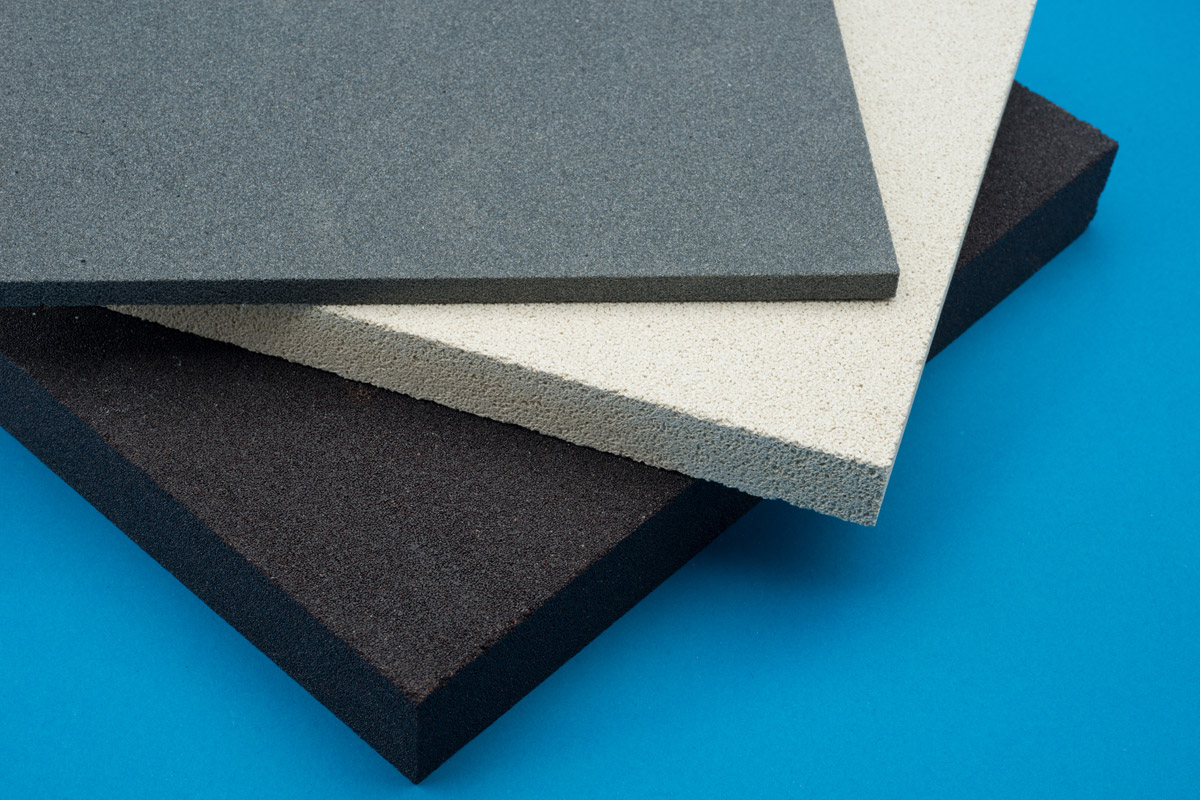
Download PDF
Case Studies:
Mantec’s tiles are especially suited to hot applications where other materials would not survive.
They are used extensively in processes such as :
- Silo/Hopper Discharge
- Powder Mixing
- Fluidised Burners
- Fluidising Conveyors
- Fluidisation Tanks
- Fluid Bed Dryers